BWS
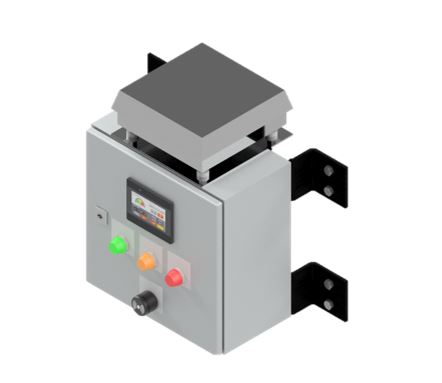
El equipo BWS está diseñado para recolectar datos específicos de cada una de las líneas de la máquina boleadora de masa en la industria de alimentos.
El sistema está diseñado para controlar una secuencia de pesaje, dirigiendo al operador mediante luces y alarma audible cuándo debe de empezar una secuencia de pesaje y de cuál hilera debe de poner la bola sobre la báscula.
El equipo se comunica con el sistema de información de la planta para tener la información del producto que está corriendo en la máquina, y de esta forma, el equipo BWS tiene la información del peso objetivo y los límites alto y bajo. Así, en tiempo real se le indica al operador cuando el peso de una de las bolas se encuentra fuera de los límites de operación establecidos.
Cada vez que un peso es registrado en el equipo BWS, es enviado al sistema de información de la planta para que se registre el peso, fecha y hora, máquina e hilera de donde proviene. De esta forma se pueden detectar en tiempo real tendencias de proceso y también cuando una máquina boleadora requiere una revisión mecánica debido a diferencias relevantes de peso entre sus diferentes hileras.
STI
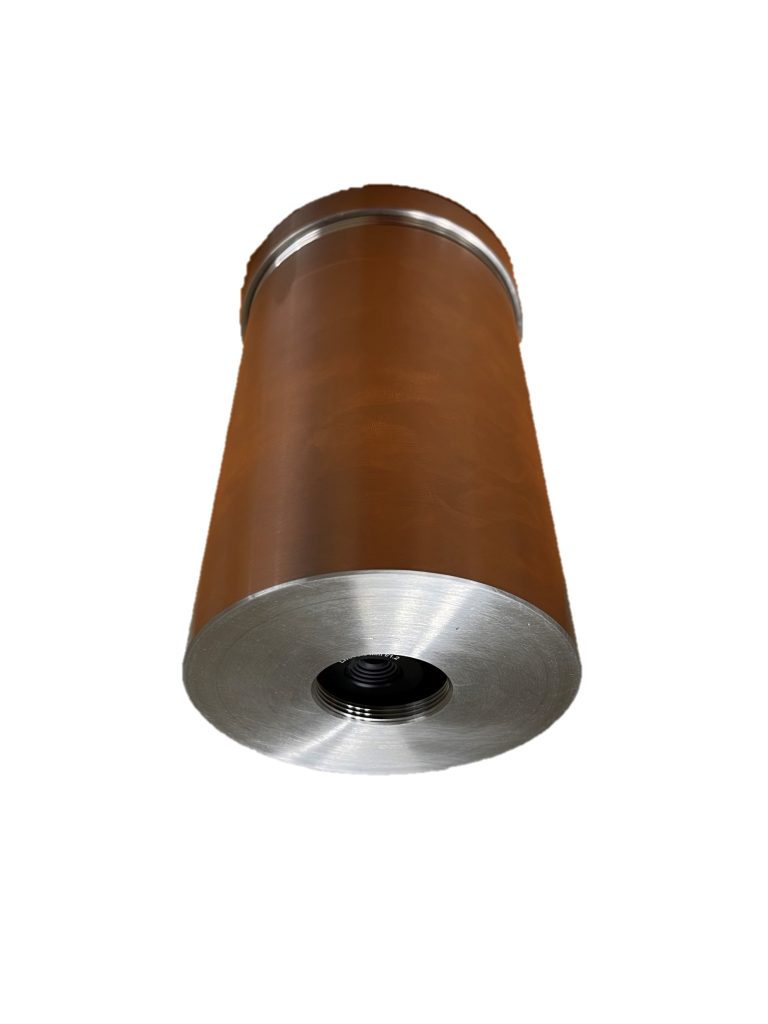
Este sistema fue desarrollado con el objetivo de poder ajustar en forma automática los parámetros de operación de la máquina donde se producen, dependiendo del tamaño de los productos. También se pueden detectar problemas que indican un desajuste mecánico.
El sistema está basado en un desarrollo propietario que analiza las imágenes capturadas por una camara industrial. El software analiza los resultados y genera cálculos utilizando algoritmos inteligentes para detectar tendencias y generar un resultado único, el cuál es retroalimentado al PLC de la máquina como la variable de control de proceso utilizando el protocolo Ethernet/IP.
DGA
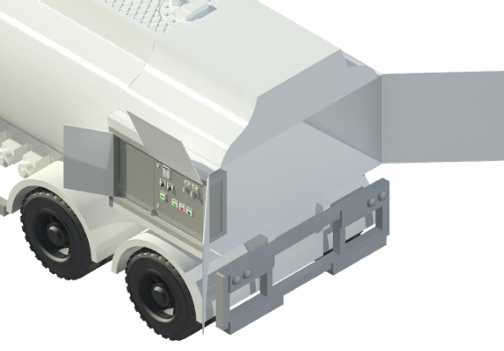
El tablero DGA, es un sistema de control que se integra a las Pipas que suministran Gases del Aire (Oxígeno o Nitrógeno). Estos sistemas tienen la necesidad de conectarse en diferentes instalaciones, donde el voltaje de alimentación puede ser de 22oVAC o 440 VAC nominales. El sistema de control detecta y ajusta de forma automaática las conexiones interna del motor de acuerdo al nivel de voltaje en cada instalación, además revisa la temperatura de la bomba criogénica así como también la secuencia de giro.
TTV
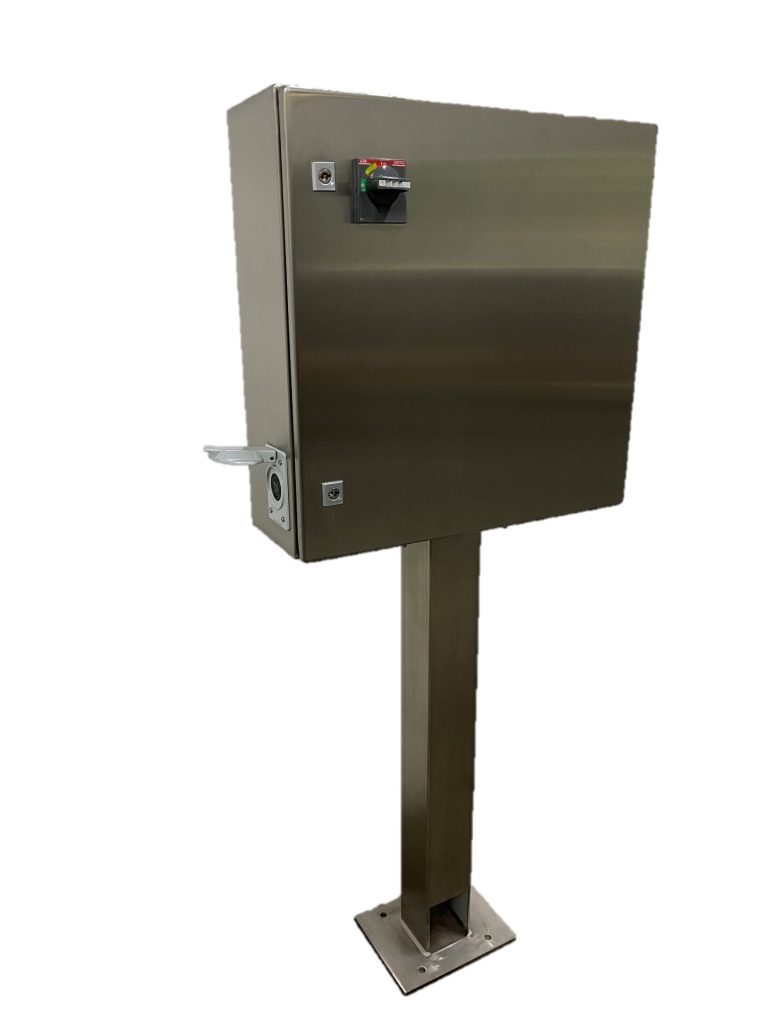
El tablero TTV es utilizado para el control y monitoreo de tanques estacionarios de CO2. Este modelo está diseñado para tanques verticales, también puede ser utilizado con tanques horizontales siempre que el nivel sea medido por presión deferencial y no por peso.
El tablero controla la presión del tanque por medio de la operación automática de elementos como válvula de estado líquido/gaseoso, compresor de refrigeración, valvula de incremento de presión o resistencias, dependiendo de los componentes disponibles en la instalación. El tablero genera alarmas locales de operación, las cuales son mostradas en una pantalla de operador instalada en la parte interior del tablero. Esta pantalla es también utilizada para ajustar los límites de operación y alarma adecuados para el sistema.
RDM-FB

El equipo RDM-FB es una versión específicamente desarrollada para estaciones de medición de suministro de gas que cuentan con un equipo FloBoss™ de EMERSON, mediante la utilización de nuestro equipo RDM-FB y el software WDM desarrollado también por nosotros, hemos implementado todo un sistema de colección de datos robusto y eficiente.
TTU
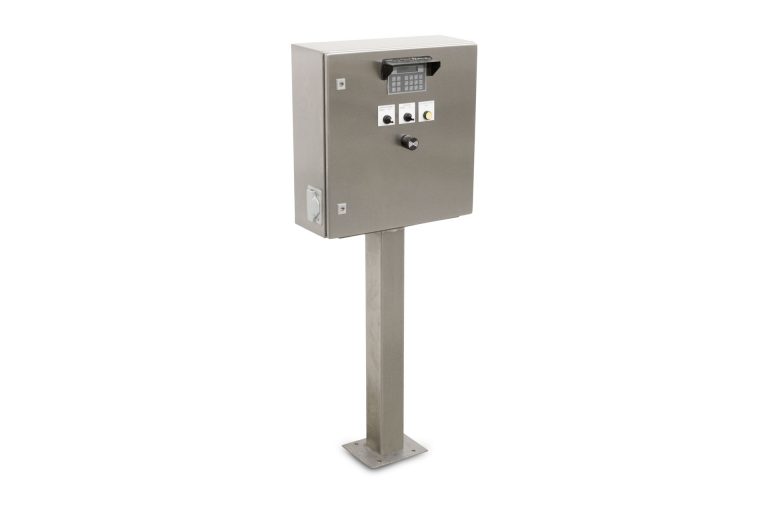
El tablero TTU es utilizado para el control y monitoreo de tanques estacionarios de CO2, tanto verticales como horizontales. El tablero controla la presión del tanque por medio de la operación automática de elementos como válvula de estado líquido/gaseoso, compresor de refrigeración, valvula de incremento de presión o resistencias, dependiendo de los componentes disponibles en la instalación. El tablero generar alarmas locales de operación las cuales son mostradas en una pantalla de operador, misma que es también utilizada para ajustar los límites de operación y alarma adecuados para el sistema.
GBH
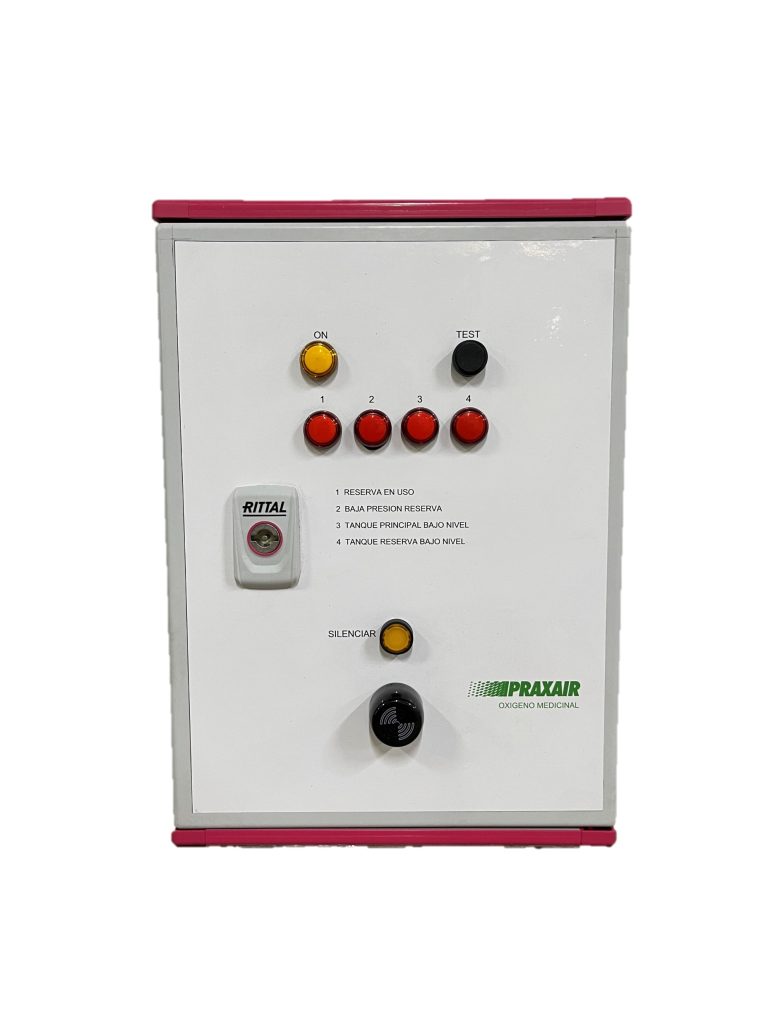
El tablero GBH es utilizado en los respaldos de oxígeno medicinal en clínicas y hospitales.
Cuando alguno de los niveles de respaldo está por debajo del límite establecido por los técnicos, el tablero indica con una luz en cuál de los respaldos se presenta el bajo nivel. Además de indicar las alarmas visualmente, también se genera una alarma audible para que el personal del hospital o clínica se percate de inmediato de la situación. La alarma audible puede ser silenciada por un tiempo predeterminado y volverá a sonar cuando transcurra dicho tiempo si la alarma todavía se encuentra activa.
PSH
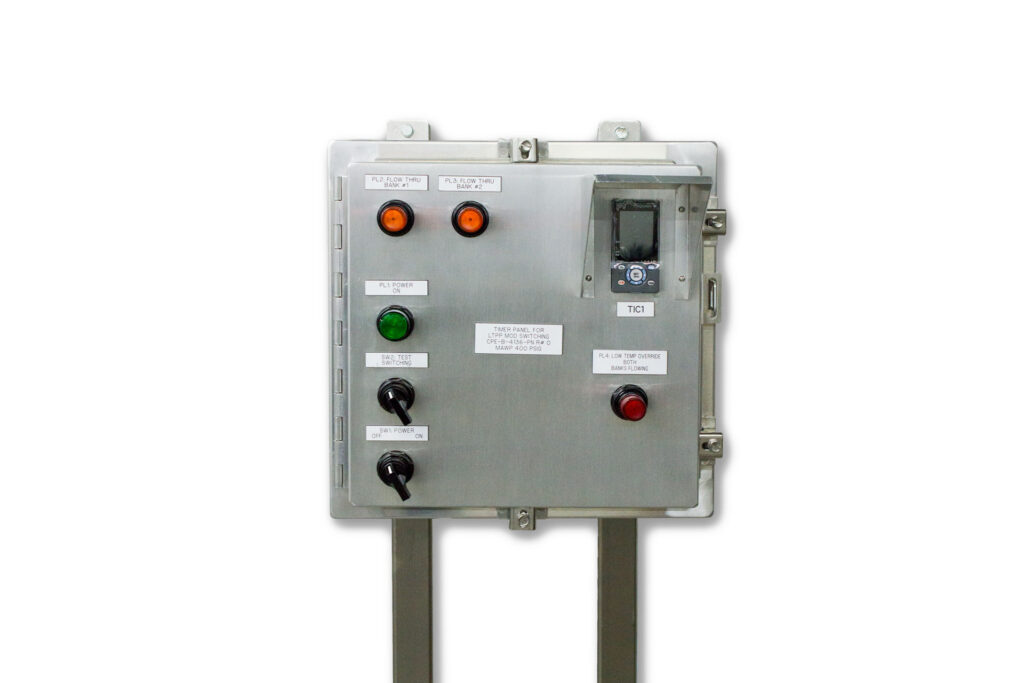
El tablero PSH fue diseñado por uno de nuestros clientes, quien nos ha encomendado su fabricación. Es utilizado en instalaciones de tanques criogénicos, para evitar la salida de producto en fase líquida, mediante la conmutación de dos vaporizadores por medio de temporizadores. Esta operación alternada permite que uno de los vaporizadores se encuentre operando mientras el segundo está en descongelación.
SGR – Generacion de Reportes en Sitio
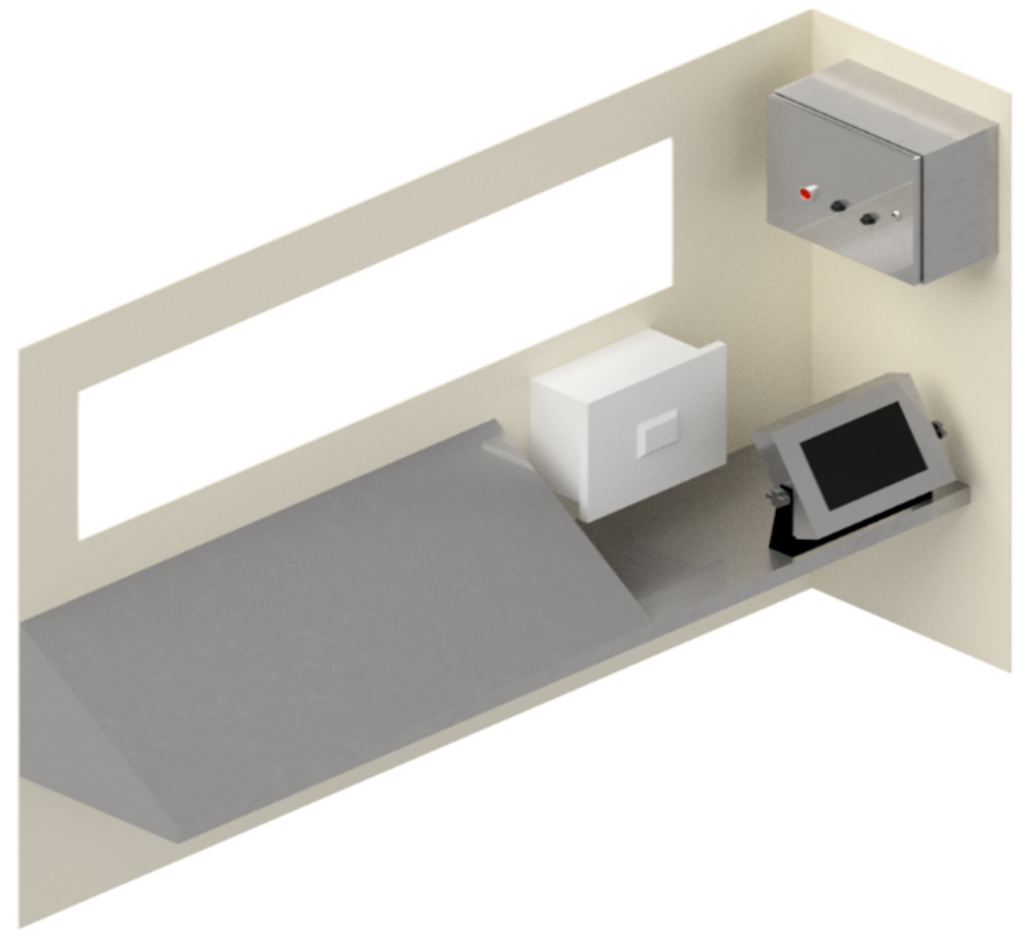
El Sistema para Gestión de Reportes o SGR está basado en una aplicación propietaria instalada en una PC tipo industrial, la cual fue montada en la cabina de las estaciones móviles de Inyección de Nitrógeno. Mediante la aplicación, el operador de la estación puede generar e imprimir en sitio reportes de servicio. Esto agiliza el proceso de facturación, reduciendo en forma importante los días demorados para la cobranza.
La adquisición de las variables de proceso (presión, flujo y consumo acumulado de N2) se realiza mediante un enlace serial (Modbus RTU) a los instrumentos de medición de las estaciones.
Además, el sistema está equipado con un módem Celular para permitir el envío, mediante correo electrónico, de la información de operación y reportes a las oficinas centrales de distribución.
Medición de Temperatura de Coraza
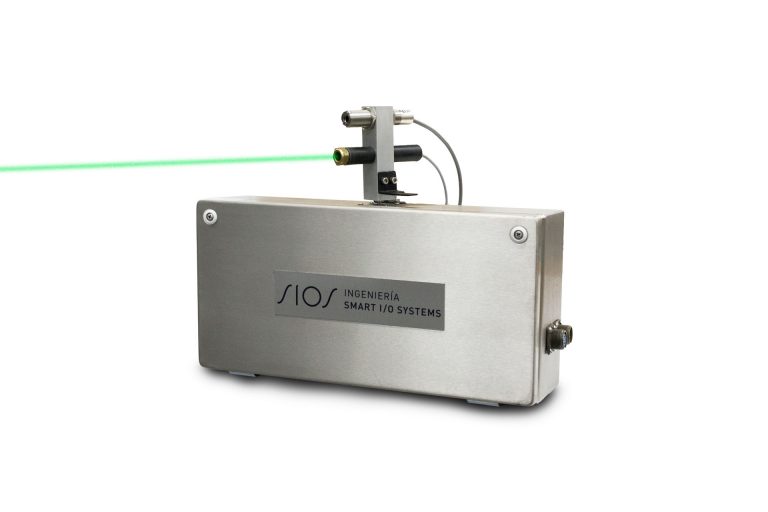
El principio de operación del sistema del Scanner IS3, está basado en el uso de la tecnología de medición infrarroja de temperatura aplicada a los hornos rotativos utilizados en la industria del reciclaje y transformación del plomo. El sensor mide las señales de radiación infrarroja a partir de las cuales se calculan las temperaturas en la superficie del horno. Las mediciones de temperatura son colectadas digitalmente por la unidad central de procesamiento y son acondicionadas y graficadas en forma del perfil de temperatura a lo largo del horno ó como una imagen termográfica completa de la superficie del horno en el monitor de la PC. Utilizando las mediciones de temperatura en la coraza del horno, las características de conductividad térmica de los recubrimientos refractarios y calculando las pérdidas de calor por radiación y convección, el sistema estima el espesor del refractario y grafica estos datos en forma de un histograma de distribución de espesores. Con esta información, el personal de operaciones puede estimar el tiempo de vida remanente, optimizando con esto la operación del horno. El sistema permite configurar hasta 4 zonas de alarma, las cuales pueden ser definidas a en cualquier punto a lo largo del horno y activan una señal de salida digital cuando la temperatura sobrepase un umbral predefinido, indicándole al controlador de proceso que anuncie una alarma o bien que tome una acción de control predeterminada. CARACTERISTICAS PRINCIPALES Supervisión en línea de la temperatura de la coraza del horno rotatorio Evitar los riesgos de daño mecánico debido a la formación de puntos calientes en la coraza del horno Detección temprana de caída de ladrillo refractario Estimación del espesor del recubrimiento refractario Evaluación de la distribución y perfil térmico en el horno